Valvole nei motori a combustione: struttura e principio di funzionamento
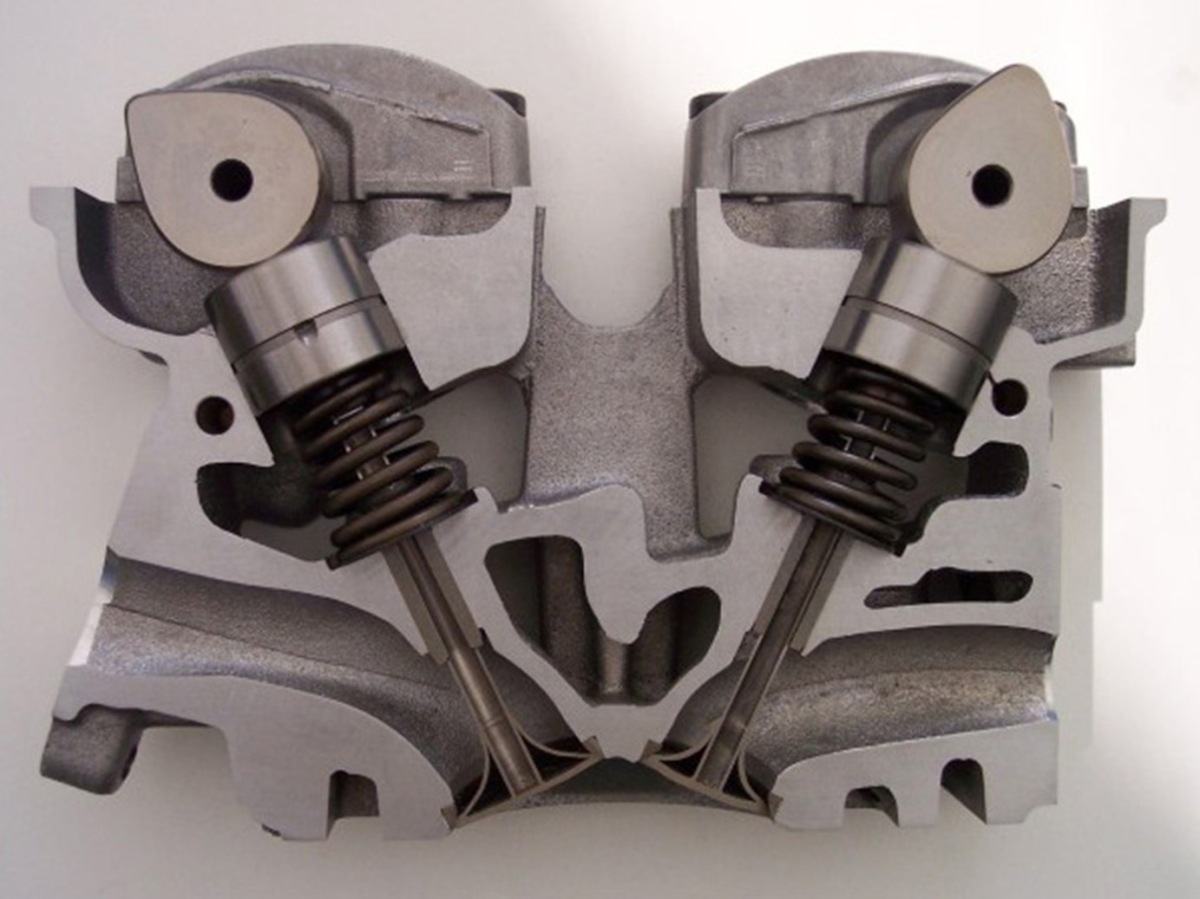
La progettazione, la produzione e il controllo delle valvole dei motori sono avvolti nel segreto. Ciò non sorprende, poiché, sebbene la valvola sia una parte relativamente piccola, essa ha un impatto decisivo sulle prestazioni del motore e sulla sua durata. I motori a combustione a quattro tempi sono sempre stati dotati di valvole, anche se nel corso dei decenni il loro aspetto, la posizione, i materiali e la capacità di carico sono cambiati.
Costruzione, resistenza termica e materiali
Da un punto di vista termotecnico, la complessità delle valvole di scarico e di aspirazione è simile a quella di un pistone: durante il funzionamento, sono esposte a carichi molto elevati, e la differenza di temperatura sulla superficie della valvola può essere calcolata in centinaia di gradi Celsius. Durante il funzionamento, la temperatura è in media di 300-600°C alla valvola di aspirazione e di 600-900°C alla valvola di scarico, sebbene la distribuzione della temperatura sia molto irregolare. Le sollecitazioni meccaniche costituiscono un carico aggiuntivo.
Gran parte del calore prodotto da un motore a combustione interna si verifica nella testata, con le valvole situate proprio al centro di essa (almeno nel caso di un motore a valvole in testa, ma ne parleremo più avanti). È quindi importante che l’area attorno alla superficie della valvola nella testata sia sufficientemente raffreddata, poiché questo è uno dei punti attraverso il quale può fuoriuscire il calore, l’altro è la guida dello stelo della valvola. Il calore nella valvola fluisce quindi verso lo stelo della valvola e viene trasferito alla testata.
Poiché il carico termico sulle valvole di scarico e di aspirazione non è lo stesso, non è necessario che siano realizzate esattamente con lo stesso materiale. Se per la realizzazione di una valvola di scarico è necessario un materiale con elevata resistenza termica, solitamente è realizzato in acciaio austenitico. Tuttavia, la sua conduttività termica è significativamente peggiore rispetto all’acciaio martensitico. Tuttavia, a volte questo vantaggio si trasforma in uno svantaggio, motivo per cui, ad esempio, una valvola con la cosiddetta struttura cava è dotata di raffreddamento al sodio. Può sembrare sorprendente, ma grazie a questa modifica la temperatura della piastra della valvola può essere ridotta durante il funzionamento fino a 100°C. L’interno dello stelo della valvola è riempito per circa il 60% di sodio, che si trasforma in un liquido a circa 97°C e in un gas a 880°C, aumentando così l’efficienza del trasferimento di calore dalla piastra della valvola allo stelo, da dove viene poi trasferito alla valvola guida stelo.
A differenza della valvola di aspirazione, la valvola di scarico può essere realizzata solo con acciai altolegati (e quindi non autotempranti) altamente resistenti al calore e alle crepe. Per decenni, un materiale popolare è stato l’acciaio al cromo-nichel-molibdeno, al quale sul calcio è saldata una piastra della valvola in una lega di cromo-nichel-manganese. La valvola di aspirazione è solitamente realizzata in acciaio al cromo-nichel, a meno che non siano applicati requisiti speciali.
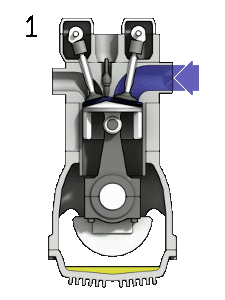
La superficie della valvola deve soddisfare requisiti completamente diversi rispetto alla zona sotto la superficie. Per l’esterno, è necessaria una superficie dura e resistente all’usura, ma l’intera valvola non può essere costituita da essa perché si romperebbe quasi immediatamente se perdesse la sua elasticità. Pertanto, nella produzione di valvole viene utilizzato l’indurimento superficiale; le superfici esposte all’abrasione, l’estremità dello stelo della valvola e le facce della valvola vengono indurite mediante l’applicazione di uno strato di carburo (cosiddetta spruzzatura di stellite) o mediante il già citato trattamento termico.
Nel caso dei motori da corsa e sportivi, capita anche che a causa del peso eccessivo delle valvole in acciaio, le valvole non riescano ad aprirsi e chiudersi abbastanza velocemente, quindi ora è possibile trovare valvole in titanio sia sul lato di aspirazione che su quello di scarico. La loro produzione è complicata e il costo è molte volte superiore rispetto a quello dell’acciaio della migliore qualità.
La piastra della molla deve essere fissata all’estremità dello stelo della valvola. Esistono molte soluzioni diverse a questo problema. Una delle forme più semplici è un perno di fissaggio inserito attraverso un foro nello stelo della valvola che trattiene la piastra della molla. Un altro modello popolare prevede due cunei di bloccaggio conici: in questo caso, la sola tensione della molla mantiene i cunei in posizione. Una soluzione più costosa ma più precisa è un sistema in cui il gioco delle valvole può essere regolato con elevata precisione utilizzando una piastra avvitata nello stelo della valvola filettato internamente.
Nel caso dei motori ad uso intensivo, l’obiettivo è prolungare la durata delle valvole, motivo per cui sono dotate di un meccanismo rotativo integrato. Quando la valvola si apre, la molla della valvola poggia sulle sfere tramite la molla a tazza del meccanismo di rotazione. Sotto carico, le sfere ruotano, azionando il piatto della molla e la valvola. Poiché questa rotazione si ripete, l’estremità dello stelo della valvola e il disco si usurano sempre in modo uniforme e rimangono privi di depositi. In pratica questa soluzione è stata modificata in modo che la piastra girevole della valvola sia stata posizionata dal lato della molla della valvola, lato testata, perché in questo modo l’inerzia che si verifica durante il funzionamento è minore. Una delle prime soluzioni di questo tipo furono i motori V8 nei camion ZIL e Mercedes-Benz.
Dimensioni e numero di valvole
L’obiettivo principale nel dimensionamento delle valvole è garantire lo scambio di carica più efficiente nei cilindri. Ciò può essere ottenuto se le valvole hanno il diametro maggiore possibile. Va notato che la dimensione delle valvole di aspirazione e di scarico ha effetti diversi sulla qualità dello scambio di carica. Quando la valvola di scarico si apre, il pistone spinge i gas di scarico fuori dalla camera del cilindro, ma quando la valvola di aspirazione si apre (nel caso di un motore ad aspirazione naturale), solo la depressione del pistone aiuta il flusso d’aria, il che significa una differenza di pressione di solo pochi decimi di bar. La necessità del diametro maggiore possibile vale in misura molto maggiore per la valvola di aspirazione, quindi vale la pena allargarla anche a scapito dell’aumento delle dimensioni della valvola di scarico. Nei motori aspirati le piastre delle valvole di aspirazione sono in media più grandi del 20% rispetto alle piastre delle valvole di scarico.
Ancora oggi la scelta del numero di valvole per un dato cilindro non è del tutto uniforme. I motori DOHC più comunemente utilizzati sono dominati da due valvole di aspirazione e due di scarico, ma esistono anche modelli a cinque e due valvole. Un buon esempio di quest’ultima è la famiglia di motori HEMI: in questo caso l’utilizzo di una valvola di aspirazione e di una di scarico è una necessità tecnica perché la camera di combustione emisferica non può ospitare quattro valvole senza ridurne drasticamente le dimensioni.